Define Zero Position Tolerance
Posted By admin On 13.09.19Mar 26, 2013 Diametrical True Position with Zero Tolerance You will have to register or login (See top or bottom of page) before you can post a message or view images: click the appropriate link to proceed. To start viewing messages, select the forum that you want to visit from the selection below.
Oleg –Typically, in the vast majority of instances a position control always requires the use of at least one datum. The only exception to this rule is if the drawing is trying to control the co-axial relationship between two separated diameters. Think of a wooden rolling pin, like you might find in the kitchen. If you wanted to ensure that the two handles of the pin were maintained, within a certain degree, were aligned on the same axis you could specify a positional tolerance with no datums.
This is somewhat of a more rare circumstance, but it does come up. The only place it’s mentioned is in the ASME Y14.5 – 2009 spec in Figure 7-59.If your situation is anything different than what I’ve described then your drawing is in error and needs further refinement.
Come back and contribute further to the community knowledge base.We cover this topic and many others in our GD&T Advanced Course. Visit our website course listings for additional information.Cheers,Matt. Ramesh –This is a quick an easy one.
If the diameter symbol is present then it indicates that the tolerance zone is a diameter and the control is applied to a cylindrical feature of size (like a hole). If the symbol is absent then the tolerance zone is the space between two parallel planes and the control is applied to a non-circular feature of size (like a tab or slot).Hope this helps. We have excellent content that goes over topics like this and many more in our GD&T Basics – Fundamentals Course. It’s an in depth self paced course that many of our customers have found to be immensely helpful.Cheers,Matt. Richard –I can’t help you with the CMM, but I can help clarify your understanding of position. The tolerance zone applies to the entire axis along the entire thickness of the feature.
For a cylindrical feature you are defining a tolerance zone of x diameter relative to datums A, B, C etc. The entire axis of the cylinder must lie entirely within this tolerance zone for the part to be considered acceptable. This includes the combined effects of translation (x, y translation) and orientation (feature tilt). Additionally, ever two point measurement of the feature must be within size for the part to be correct.I hope this clarifies things. If now, feel free to come back and ask additional questions.Cheers,Matt.
Comment Guidelines:We are grateful to have so many people using our website each day to learn more about GD&T. We would love to hear your anecdotes or experience using GD&T as well as address any suggestions or feedback about the content on this page.We do not answer questions about GD&T interpretation or application in the comment section.
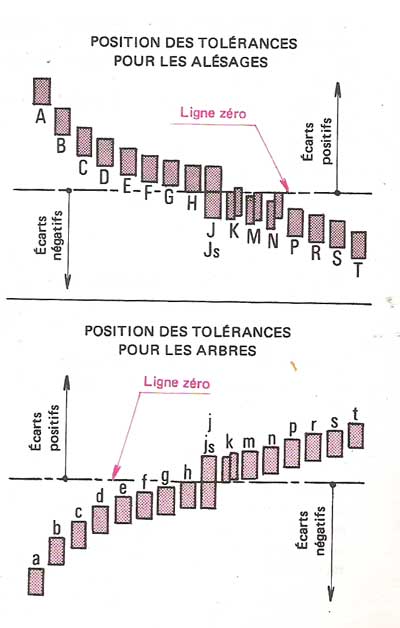
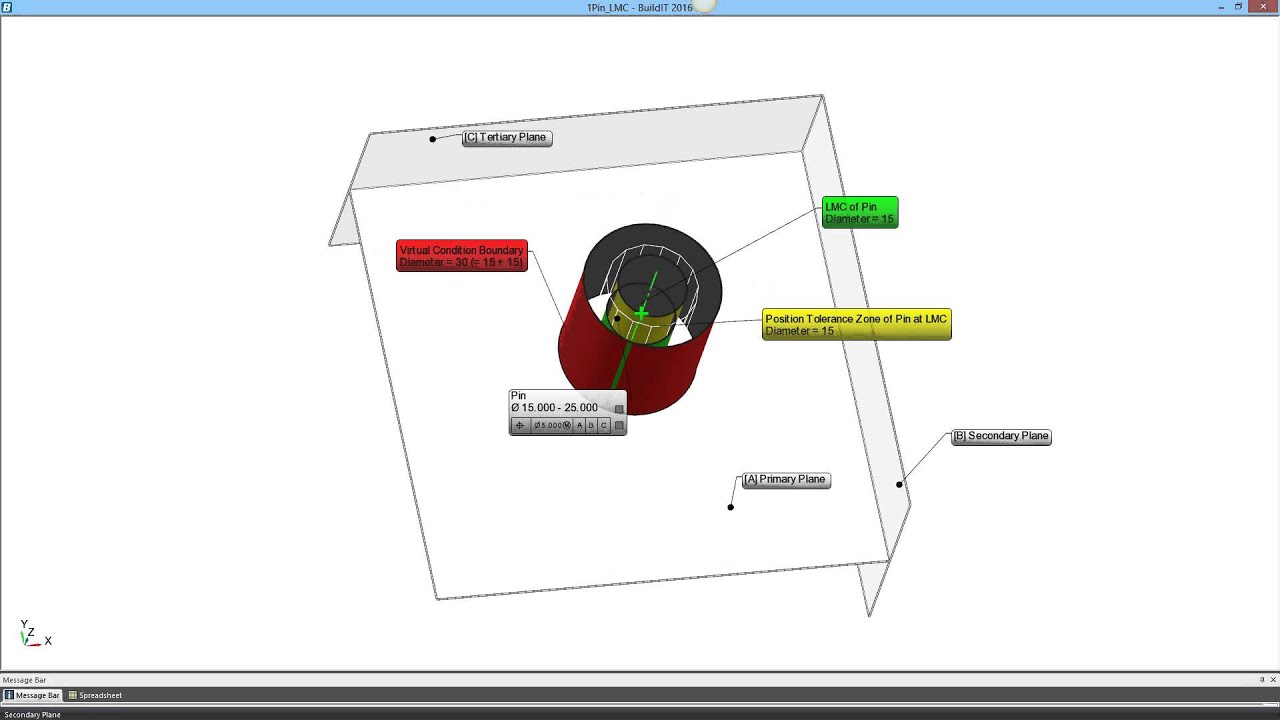
However, if you are getting stuck with how to apply or interpret GD&T, be sure to check out our. Our courses come with our GD&T Forum where our ASME Senior-Certified Experts can directly help you work through all of your interpretation or application issues. Thanks again for using the #1 GD&T online resource!I have read and accepted the.
Hello,I have just ran across a drawing with a diametrical true position tolerance of '0' (zero), with an M with a circle around it right next to it (for MMC). In the rest of the feature control from, it has an 'A', then a 'B' with MMC, then 'C' with MMC. Datum A is a face, Datum B & Datum C are holes that are the same as what is being toleranced (there are twelve holes). The diameter tolerance of the hole is 8.5mm +1mm/-0mm.I'm not the greatest GD & T guy (hence, the post), soooo does this mean I would only get tolerance if I held the diameter larger than 8.5mm because of the MMC callout? I am trying to determine the machining process for this part and need to know how feasible this tolerance is to hold.or what tooling/size I should use/try to hold.
Be my princess party glenn. If I held the diameter at 9.2mm, how far could I be off from the mean dimension? I've never seen a '0' for a true position tolerance.Thanks for any help.

Define Zero Position Tolerance Test
Welcome to the forum and this issue is not a strong suit for me but a couple of observations. A zero tolerance is impossible to achieve. That would depend on the measuring instruments involved.
Are we talking a wooden rule, a micrometer, a MMC, a microscope, and scanning electron microscope, and Atom watching thingy that IBM used to write their initials in Atoms?Soo if your customer has zero tolerance on the drawing I suggest you send it back to them with a 'get real' kinda statement.Next, as a young draftsman many years back it was hammered into me to always put 'Never assume, if in doubt ask' on all drawings (before pre-printed drawing sheets, yes, I am, that old). I suggest you take this advice and ask the customer. Soooo does this mean I would only get tolerance if I held the diameter larger than 8.5mm because of the MMC callout?Yes, true. Thank you for the replies.I just want to make sure I'm understanding this fully.I was planning on cutting these diameters to 9mm, so those diameters along with Datum B & C will be 9mm diameter, so the size divergence is 0.05 mm, does that calculate to 1.0 mm maximum allowed positional tolerance for the hole features?
Discrimination Rule Of Thumb
(0.50 (diameter over MMC) + 0.50 (Datum B & C divergence).So the tolerance is zero at MMC, but due to the large diameter tolerance of the primary feature and datums, (the size is stated at 8.5mm +1mm/-0mm) if we hold the holes 0.5mm big from the called-out diameter (holding 0.5mm over the called-out 8.5mm is really the mean size in this case), we have a fairly open diameterical true position then? (1.0mm)If the size was stated as 9mm +/- 0.5mm with the tolerances spelled-out the same way, then I'd have to drill the diameters to the absolute high side (9.5mm) in order to get the 1.0mm true position tolerance, correct?Thanks. I was planning on cutting these diameters to 9mm, so those diameters along with Datum B & C will be 9mm diameter, so the size divergence is 0.05 mm, does that calculate to 1.0 mm maximum allowed positional tolerance for the hole features? (0.50 (diameter over MMC) + 0.50 (Datum B & C divergence).Yes, this is correct.I'm a little wary of how you expressed the bonus tolerance achieved from the datum features.If each Datum (B & C) diverge 0.025 each -.025 +.025 = 0.5 total bonus tolerance from MMC.If each Datum (B & C) diverge 0.50 each -.5 +.5 = 1.0 total bonus tolerance from MMC. I think we have to be careful, because if datum features B and C are larger than 8.5, those enlargements do not both translate into direct additional tolerance for the hole in question. So unless I'm reading your post wrong, Kelly, I would disagree.If datum feature B is enlarged but datum feature C stays at 8.5, then the position tolerance of the hole being measured does not grow in a circular fashion. Think about it: if one datum hole (B) is big but the other is not, then the looseness around B only allows the part to swivel in a rotational manner.
Position Tolerance Example
And if both holes are enlarged to 9 mm, that doesn't mean the the extra half-millimeter of growth on each translates into 1 mm of extra position tolerance, because together there is only one movement of the partFYI - this extra slop around the datum is usually called 'shift tolerance,' to distinguish it from 'bonus tolerance,' which is only the slop taken from the first MMC modifier. Bonus tolerance is always OK to directly add into the position tolerance number.
But shift tolerance can only be thought of as additive if there is one datum being modified, and if it acts in the same direction as the hole being positioned. I think we have to be careful, because if datum features B and C are larger than 8.5, those enlargements do not both translate into direct additional tolerance for the hole in question.
So unless I'm reading your post wrong, Kelly, I would disagree.Well, you’re right to disagree with me John-Paul – as you’re correct. My answer to the op cuts a lot of corners and is functionally not “most correct”.It can be challenging to describe the effects of size divergence from MMB for multiple datum features without a function gage.Now, if the op had a single datum that was coaxial with the datum feature, my answer would be “more correct”.Hopefully, the op has either a CMM or a qualified functional check gage to verify the as-built features and the effective datum shift. Thank you for the replies! And yes we do have a CMM to check our parts but this is in the quoting stage and I never have seen a '0' (zero) tolerance expressed for a diametrical true position feature. So I was just making sure that if I drilled the hole larger than the called-out size for the diameter (8.5mm +1mm/-0mm), that I truly would have a tolerance I could live with. So, I believe now, after reading your replies, that if we plan on cutting these at 9mm with a solid carbide drill, we shouldn't have any problems holding the true position tolerance.Thank you again for the helpful information!- Paul.